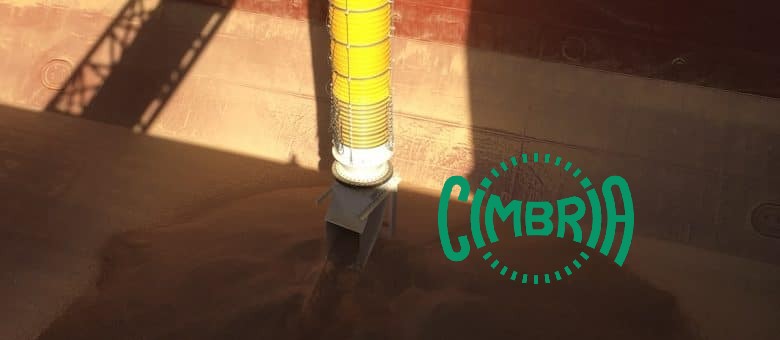
Cimbria on ottanut tehtäväkseen modernisoida eri teollisuuden alojen lastausasemia ja on onnistunut kehittämään erilaisia lisävarusteita nykyisiin lastauspalkeisiin. Kehitystä on tapahtunut esimerkiksi lannoitteen lastaamisessa junavaunuihin. Myös laivalastaukseen on kehitetty uusia apuvälineitä kuten esimerkiksi nivelakselilla varustettu lastauspalje, jonka avulla palje saadaan pysymään paikoillaan lastauksen aikana. Alla olevasta artikkelista voit lukea lisää lastauspalkeiden kehityksestä.
New Accessories Enhance the Moduflex Range of Loading Chutes
As an ongoing process, a number of new accessories and loading solutions have been added to the Cimbria Moduflex range of loading chutes. Some of these solutions have been constructed to solve a specific task in a loading application, whilst others have been designed for more general use to form part of the constantly growing range of accessories that can be offered to customers.
In several cases, Cimbria has been the “first mover” in terms of developing solutions for modernizing loading stations within industrial sectors that hold great potential. One example of such development is the optimization and upgrading of systems for loading fertilizer into train wagons. Two of these solutions are described in the following articles.
Cardan joint for ship loading
On several occasions, Cimbria has designed and supplied a cardan joint for ship loading chutes on various projects. Many ship loading applications require a conveying boom with the ability to pivot up and down in conjunction with the loading scenario. The purpose of the cardan joint is – in all instances – to keep the loading chute in a vertical position.
This may apply in the loading situation, where due to a difference in the size of the ships or due to large differences in tidal water, there is a need for different heights of the loading chute position. However, it is also required in the parking situation. It is clearly necessary to keep the loading chute in a vertical position during loading in order to enable the correct flow of the product, whilst keeping the wear factor on the inlet and guide cones of the loading chute to a minimum.
Earlier, the design and construction of these cardan joints had very much taken place as one-off solutions based on Cimbria’s vast experience of manufacturing such equipment. These units have been constructed with a combination of Cimbria’s knowledge and the demands of the customer, whilst taking into account the specific parameters of the location, product and wishes of the end user. This has spawned a desire to develop a standard programme of cardan joints in the product range in order to quickly and efficiently be able to offer a complete solution including cardan joint and loading chute. Nevertheless, it will of course still be possible to offer bespoke solutions in terms of cardan joints in cases in which the standard range does not suffice.
Furthermore, in this development phase it was decided to design a cardan joint for the existing V-series, as well as the new A-series of loading chutes.
Focus was applied to two factors that needed to be achieved in the development project: one was to achieve as low a height as possible and the other was the ability to insert various wear plates in the hopper of the cardan joints. Both these goals were achieved, in addition to a decrease in weight also being realised. This means that the cardan joint can be easily adapted to virtually any dry bulk material, with the option of inserting wear plates in standard steel, Hardox or Vautid. Furthermore, it means that maintenance of the cardan joint is very service friendly and replacement downtime is relatively short.
The cardan joint can naturally also be constructed with all product contact in stainless steel, if this is required by the end user. The cardan joint is available for all sizes of chute and includes a counterbalance system.
Radial trimmer for ship loading
The latest addition to the range of accessories for the loading chute for ship loading is the radial trimmer. This trimmer comes in a variety of options depending on the application and the requirements of the end-users.
The radial trimmer is fitted to the outlet of the loading chute, and can be used permanently or intermittently as and when required. The main purpose of the radial trimmer is to ensure that the hold of the ship is filled under deck sides with the minimum of machine movements, thereby maximizing the stowed volume. The radial trimmer can be supplied in a stainless steel version, or constructed with wear-resistant steel plates. An adjustable counterbalance is part of the radial trimmer, which ensures a stable loading situation.
The radial trimmer is mounted on a precision slewing ring with electric motor drive controlled either from the operators’ cab or through the use of a hand-held remote pendant control station.
Over the last couple of years a number of orders for loading fertilizer into train wagons have been delivered. A particular challenge when loading into train wagons is always the variety of hatches present on the different wagon types, although nearly all of them are rectangular in shape. In order to ensure dust-free loading, it is necessary to cover the hatches, and for this purpose a number of special outlets have been implemented.
After receiving information from the customer with regard to the size of the hatches on the train wagons to be loaded, a rectangular steel plate is designed in a way that will contain the dust inside the wagon.
These outlets can be combined with either FlexClose, which seals the outlet when the loading chute is not in use, or with FlexFill, which is designed to disperse the product into the train wagons to ensure maximum filling. In addition, the loading chutes can be configured for operating in environments in which temperatures can fall to -40° C.
Apart from the added value to the customer of filling the train wagons to the maximum capacity, the system provides operators with a dust-free and thereby clean working environment.
A customer has developed a concept for quick loading of fertilizers such as DAP, MAP and all kinds of NPK into special closed containers.
Cimbria Unigrain was asked to deliver six chutes for this new project. Initially, price was a key factor, as we were competing against a couple of other loading chute suppliers. In the end, Cimbria Unigrain managed to convince the customer that we had a better technical solution, and we won the order.
The customer was satisfied with the delivery of the first six chutes, subsequently ordering another six chutes with more features. Cimbria therefore agreed that the customer should visit them, and together they developed a K400THEX/4 in AISI304 with FlexFill and GOST and ATEX certificates.
Furthermore, the motors were to be made in cast iron due to the fact that the fertilizer is highly corrosive.
The customer had an issue with 6-7 cubic metres of empty space in the container at that time. Another issue was the structure of the granulate, with the customer particularly concerned that rough treatment could damage the granules against the walls of the container.
After developing the chute with a new wing for FlexFill, the amount of material loaded into the container was increased by several percent, whilst the structure of the granulate remained intact.
Initially, the customer was able to load 1 million tonnes per year, but with a declared goal to load 1.5 million tonnes per year.
In some applications, problems with dust can be solved by spraying water onto the product during loading. A prerequisite is of course that the product can withstand the water and does not change characteristics during the process. Examples of products where this is viable are coal, coke and iron ore. The advantage of this method is that no aspiration system is required and the risk of dust explosion is minimized.
This water spray system has been implemented and supplied on both smaller loading chutes, typically for loading into open trucks/dumpers, as well as for bigger stockpiling chutes. The systems consist of a manually operated ball valve or a valve fitted with a solenoid valve that is connected to the water supply. By opening the water flow when loading starts, the water runs through a hosepipe along the loading chute and into a spray ring at the outlet. This spray ring is fitted with a number of nozzles, depending on the size of the outlet. The water hose is either a spiral hose or is mounted on a hose reel, so it will follow the chute when it is extended and retracted. When loading is complete, the water supply is switched off and the chute can be retracted.
The system can be built into loading chutes for open trucks, as well as for ship loading applications.
About Moduflex – Safety and clean environment in a single product.
Cimbria Moduflex loading chutes are designed for dust-free outloading of dry bulk material. The loading chutes can be supplied for tanker trucks, flatbed trucks, open and closed rail wagons, and containers. The chutes can be manufactured in a more sturdy construction for shiploading, stockpiling and warehousing, depending on customer requirements with regard to heavy-duty performance, long-term durability and high capacities. The product range covers all sectors where dry bulk products are handled, from agricultural products to industrial commodities and raw materials.